In the realm of industrial automation where micron-level precision meets harsh operating environments, contact probes (pogo pins) and their mating receptacles have emerged as unsung heroes. These components form the physical interface layer that bridges the gap between digital control systems and the physical world.
1. The Nerve Endings of Automated Systems
Modern automation relies on continuous electrical signal integrity. Spring-loaded contact probes with gold-plated tips (typical resistance <30mΩ) provide:
- High-Cycle Reliability: Rated for 1 million+ mating cycles (per MIL-STD-1344 Method 3036)
- Micro-Ohmic Stability: Maintain contact resistance variance under ±5% after 10k cycles
- Self-Cleaning Action: Sliding contact wipes surfaces clean (critical in metal particle-rich environments)
Case Study: In automotive ECU testing rigs, custom 256-pin probe arrays achieve <0.3ms signal latency during 24/7 operation.
2. Enabling Modular Automation Architecture
The rise of Industry 4.0 demands reconfigurable production lines. Magnetic-lock receptacles with IP67-rated housings allow:
- Tool-Free Component Swaps: Change end effectors in <90 seconds (vs 15+ minutes for hardwired systems)
- Hot-Swap Capability: Maintain power continuity during sensor module replacements
- Mixed-Signal Integration: Hybrid connectors combining 10Gbps data lanes (Impedance 100Ω ±10%) with 20A power contacts
Robotics Example: Collaborative robot wrists integrate 12-channel probe rings transmitting torque/temp data while delivering 48V servo power.
3. Overcoming Harsh Environment Challenges
Automation components must survive where humans cannot:
Threat | Probe/Receptacle Solution | Performance Standard |
---|---|---|
Vibration (15g) | Coaxial spring design | MIL-STD-810H Method 514.7 |
Thermal Shock | Beryllium copper alloys | -55°C to +175°C operational |
Chemical Exposure | PTFE insulation sleeves | Resists IP69K washdown fluids |
Food Industry Application: Stainless steel probes with antimicrobial coatings withstand daily caustic cleaning cycles in packaging lines.
4. Data Integrity at Industrial IoT Scale
As factories generate terabytes of sensor data daily, contact interfaces become data highways:
- EMI Shielding: Triaxial contacts achieve 80dB attenuation up to 6GHz
- Cross-Talk Control: Grounded pitch as tight as 0.4mm in high-density arrays
- Fault Detection: Embedded microswitches detect incomplete mating (error code 0xE3 in PLC logs)
Smart Factory Implementation: Vibration monitoring probes with integrated MEMS sensors stream real-time FFT data through modular receptacles to edge AI gateways.
5. Economic Impact of Optimized Contacts
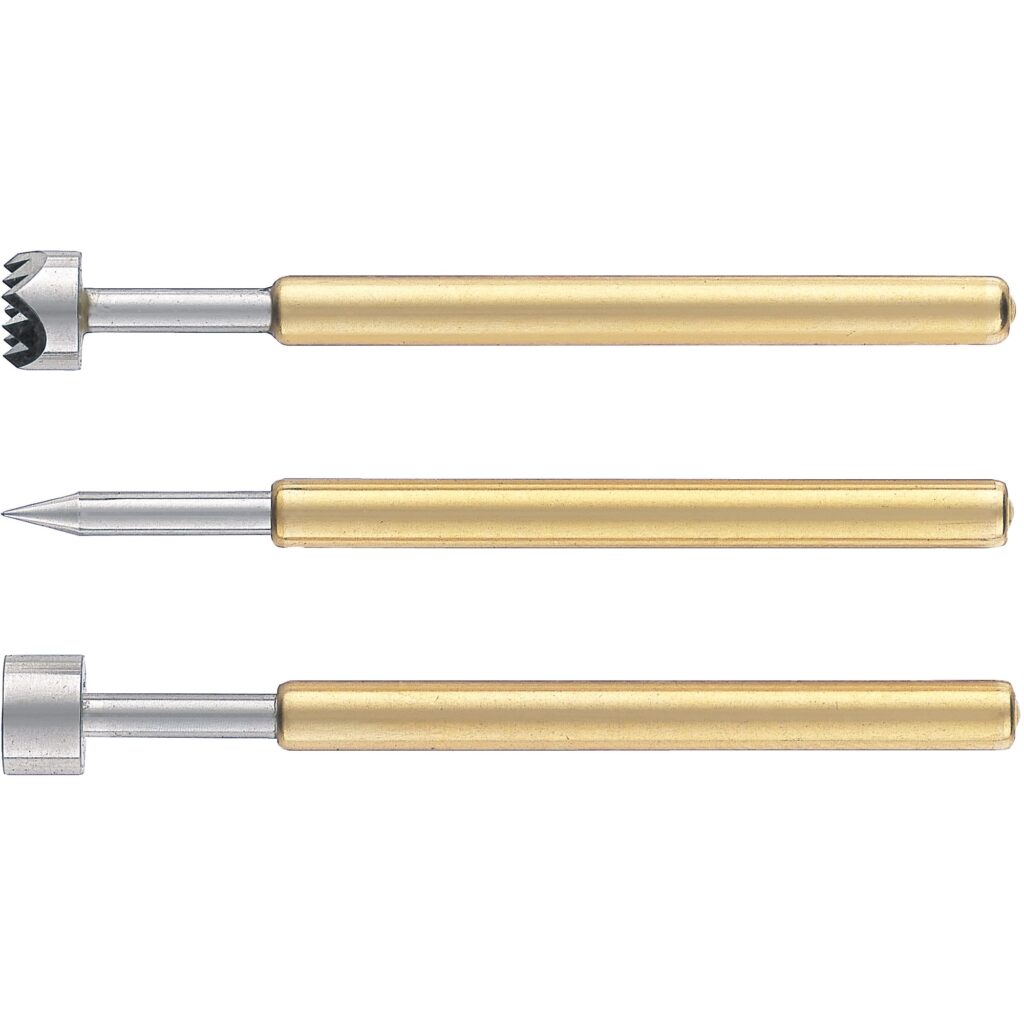
A lifecycle cost analysis reveals:
- Downtime Reduction: Quick-connect probes cut changeover time by 73% (BMW Leipzig Plant data)
- Maintenance Costs: Self-cleaning probes extend calibration intervals from weekly to quarterly
- Scrap Rate Control: Gold-nickel plating prevents false opens in weld monitoring circuits
ROI Example: Semiconductor test handler probe card upgrades delivered 218% ROI in 11 months through improved yield monitoring.
The Future: Smart Contact Systems
Next-gen probes with embedded microchips (ISO/IEC 21434 compliant) will enable:
- Predictive wear analytics via contact resistance trending
- Auto-adjusting normal force based on temperature readings
- Cryptographic authentication of tooling attachments
Conclusion
In an era where milliseconds and microns determine manufacturing competitiveness, contact probes and receptacles have evolved from simple connectors to intelligent system enablers. Their continued innovation sits at the heart of achieving truly resilient, reconfigurable, and data-driven automation ecosystems.